The complexity of electrical and mechanical engineering
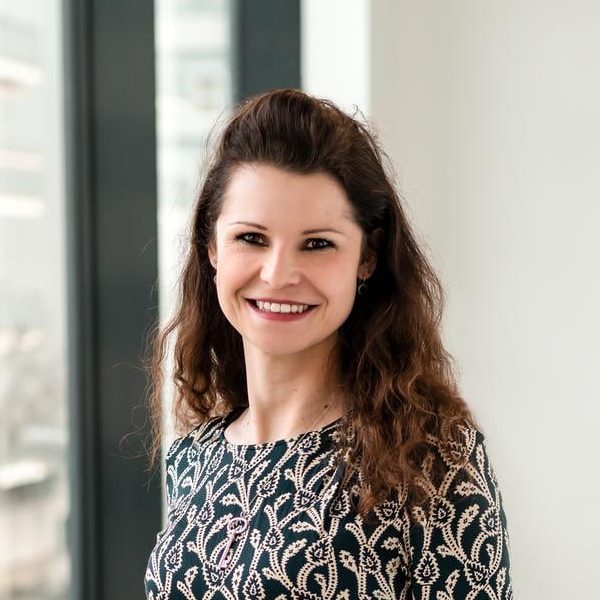
From Miriam Schulze
CEO BAYOOMED
As someone who has worked on both hardware and software for medical devices, I’ve come to understand the profound differences between these two fields. While software development certainly has its challenges, hardware development, particularly in the realm of medical devices, presents a unique set of difficulties that make it significantly more complex.
Here, I will delve into why hardware R&D for medical devices is so much harder than software, illustrated with real-world examples, including the development of the NeoDoppler from Cimon Medical.
Physical constraints
Unlike software, hardware development must account for physical limitations and environmental factors. For instance, thermal management is crucial in hardware design. Overheating can not only damage the device but also pose safety risks to patients. Overheating can not only damage the device but also pose safety risks to patients. In the case of the NeoDoppler, ensuring that the sensitive Doppler ultrasound technology operated within safe temperature ranges required meticulous thermal management solutions.
Electromagnetic compatibility (EMC) is another critical aspect. Medical devices must not interfere with other electronic equipment and must be immune to electromagnetic interference. The NeoDoppler needed extensive EMC testing to ensure it would not disrupt or be disrupted by other critical medical equipment in a neonatal intensive care unit (NICU).
Mechanical durability is equally important. Devices must withstand physical stresses, such as drops, repeated use or just cleaning. For the NeoDoppler, ensuring that the device could endure the demanding environment of a NICU involved selecting the right materials, determine compatible cleaning agents and a rigorous mechanical testing to confirm it could handle daily usage without compromising its functionality.
Prototyping and Testing
Iterating on hardware prototypes is significantly more time-consuming and costly compared to software. Each hardware prototype requires fabrication, which can take weeks, followed by meticulous testing to ensure compliance with stringent medical standards.
This usually means each prototype iteration involves creating detailed models, assembling components, and conducting extensive tests to meet medical standards. Each failure in testing means redesigning components, which is both time-consuming and expensive.
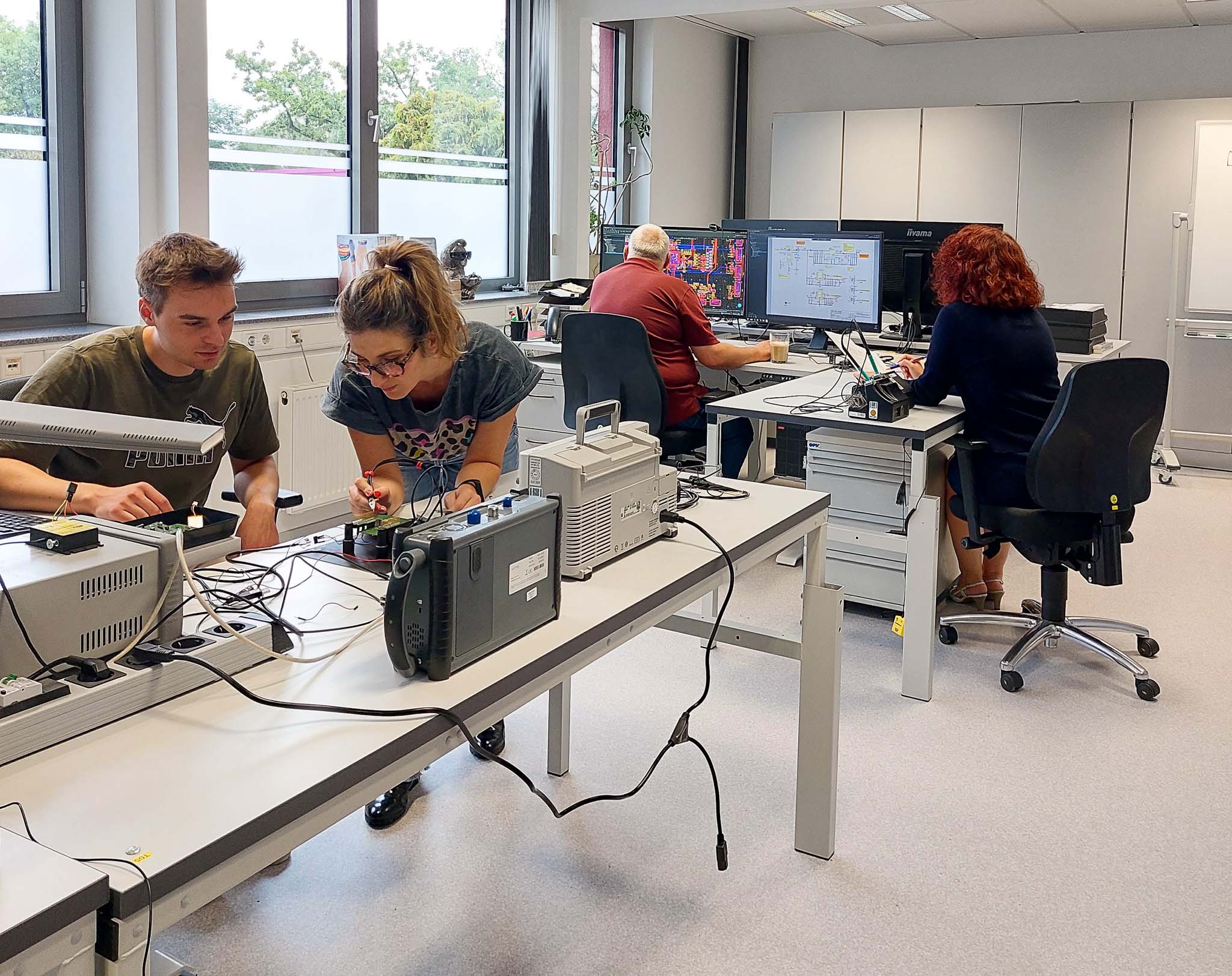
A look at the electronics development department at the YOOme partners of Mechatronic GmbH.
Interdisciplinary knowledge
Successful hardware development requires a diverse set of skills, including mechanical engineering, electrical engineering, and materials science, in addition to software skills. Coordinating among various disciplines to ensure seamless integration is a formidable challenge.
Developing the NeoDoppler involved integrating advanced Doppler ultrasound technology, precise electronics, and robust mechanical design into a compact and user-friendly device. This required close collaboration between different teams to address issues like signal integrity, power consumption, and ergonomic design.
Regulatory hurdles
Medical devices must adhere to rigorous regulatory standards and undergo thorough evaluations by notified bodies. This conformity assessment process is extensive and requires detailed documentation and robust quality management systems.
For the NeoDoppler, navigating the regulatory landscape involved providing comprehensive documentation covering every aspect of the device’s design, manufacture, and testing. Achieving regulatory approval required rigorous validation and verification processes to meet standards set by regulatory bodies.
Manufacturing complexities
While software will be just deployed to a platform scaling from a HW-prototype to mass production involves overcoming numerous manufacturing challenges. Ensuring consistent quality, managing supply chains, and controlling production costs are critical aspects that add to the complexity.
Manufacturing a device at scale required setting up specialized processes to maintain high precision and reliability. Establishing stringent quality control measures and working closely with suppliers to ensure the availability of components were crucial steps. Any deviation in the manufacturing process would result in significant delays and increased costs.
Conclusion
While software development is undoubtedly challenging, the complexities of hardware R&D for medical devices make it a far more arduous endeavor. From dealing with physical constraints and prototyping hurdles to navigating regulatory requirements and manufacturing complexities, hardware development demands a multidisciplinary approach and a high level of expertise.
The impact of successfully developing these devices, however, is immensely rewarding. The difference they make in patient care and health outcomes, as demonstrated by devices such as the NeoDoppler, underscores the importance of persevering through these challenges. For those venturing into this field, understanding and preparing for these hurdles can make the journey more manageable and ultimately more successful.
How have you tackled the challenges of hardware development in your projects?